Coolidal Mill For Liquid Coal
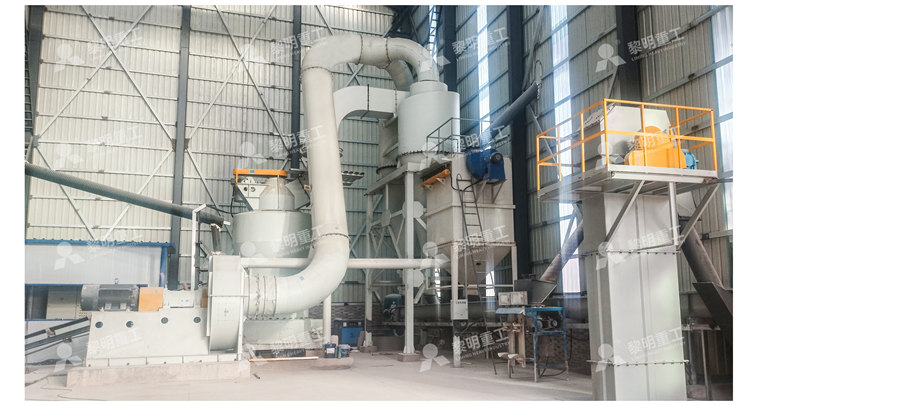
Improving oxidized coal flotation by colloid mill pretreatments
2017年3月8日 Colloid mill attrition can remove the oxidized layer from oxidized coal surface The effects of colloid mill gap space and milled pulp density were investigated according to the flotation response It was found that both particle size reduction and flotation recovery The IKA MK 2000 is a highperformance inline colloid mill capable of performing wet and fine milling of tough and grainy raw materials The MK 2000 is especially suitable for the production of colloidal solutions or extremely fine emulsions Colloid Mill MK Inline dispersers / Mills, 1 天前 COLLOID MILL APPLICATION PROCESS Procedural Operation Applications of Colloid Mill Machine A colloid mill is a machine that is used to reduce the particle size of a solid in suspension in a liquid, or to reduce the Colloid Mill Colloidal Mill Machine, Colloid Mills are your best solution for particle deagglomeration and primary particle size reduction Commonly used in the chemical and personal care industries, colloid mills are used to grind the primary particles of solids in a Colloid Mills Colloid Mill Systems Sonic Mixing
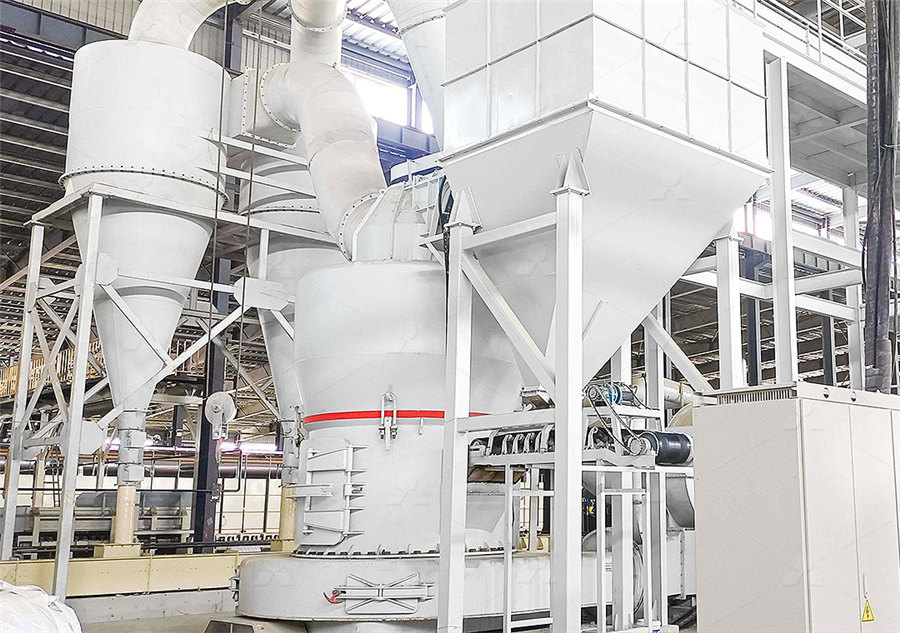
Solid–liquid separation technologies for coal ScienceDirect
2023年1月1日 This chapter discusses current developments and latest applied solid–liquid separation (SLS) technologies and equipment used for coal The chapter commences with 2018年12月3日 Colloidal interactions play an important role in mineral processing Developments of various techniques allow us to study the phenomena involving colloidal interactions, including slime coating, homo Recent Advances in Studying Colloidal 2023年10月16日 Colloid mills are used to reduce the size of solid particles suspended in a liquid or semisolid medium The highspeed rotorstator action generates intense shear forces that COLLOID MILL Bombay Pharma2005年3月8日 Abstract In a colloid mill utilizing a rotating and a stationary plate, a high shear field exists Particles rotate, generating a lift force moving them to the rotating plate When Colloid Mills: Theory and Experiment ResearchGate
.jpg)
Kinetic modelling of coking coal fluidity
2020年3月10日 Coal plasticity is a phenomenon directly affecting the creation of coke structure It is very much a time and temperaturedependent transformation of the coal matrix, which allows changing the physical phase from solid to 2022年11月30日 Colloid mill is a machine used in the disintegration of solid particles or droplet size of a liquid present in suspension or emulsion The machine consists of an inlet (which is subjected to a tremendous shearing Colloid Mill: Operating Principles, components, Sols are colloidal systems where solid particles are dispersed in a liquid medium Due to Brownian motion, sols have smaller particle sizes that do not settle over time Gels consist of a continuous solid network throughout a liquid medium Colloids: Definition, Characteristics, Types, and 2023年1月1日 14 Solid–liquid separation technologies for coal Author links open overlay panel Gotz Bickert Show more Outline belt, chamber, tube, vibrated bed, pneumatic, pulsed combustion, fluidized bed, vibratory, mill type shaft to moving bed dryers, which could be either tempered with ambient air or with gas/exhaust recirculation while the Solid–liquid separation technologies for coal ScienceDirect
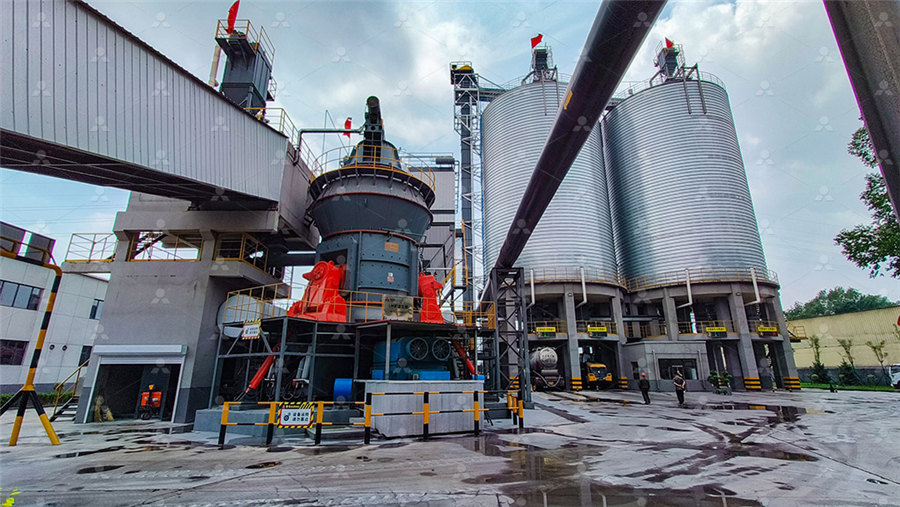
Thin liquid film drainage mechanism for bubble − particle
2024年3月15日 Thin liquid film drainage mechanism for bubble − particle attachment interactions in the lowrank coal flotation in the presence of salt and surfactants The lowrank coal samples were first crushed by a jaw crusher and then drygrinded using a mechanical ball mill After that, the particles were dry sieved to different size fractions A colloid mill is a machine that is used to reduce the particle size of a solid in suspension in a liquid, or to reduce the droplet size of a liquid suspended in another liquid +9179; sales@prismpharmamachinery; MENU MENU About; Products Mixers;Colloid Mill Pharmaceuticals Machinery2024年3月15日 The lowrank coal samples were first crushed by a jaw crusher and then drygrinded using a mechanical ball mill After that, the particles were dry sieved to different size fractions (containing 0–0074 mm, 0074–015 mm and 015–025 mm three parts) Obviously, the stability of the liquid film of coal particles after KCl salt Thin liquid film drainage mechanism for bubble − particle ``` coolidal mill for liquid coalColloidal Fuel Dispersions using Coal,Petroleum Coke and technologies have led to the development of colloidal fuel dispersions using coal,petrolgitsrht
.jpg)
CoaltoLiquid Technology an overview ScienceDirect Topics
Economic analysis of unconventional liquid fuel sources Mehmet Erturk, in Renewable and Sustainable Energy Reviews, 2011 221 Coal to liquid (CTL) Coal is a solid fuel with high carbon content compared to liquids The current liquid fuels which are consumed for the transportation purposes have hydrogen content around 12–15%, whereas coal contains only 5% typically [1]2014年1月1日 Two mill systems are employed for most coal grinding applications in the cement industry These are, on the one hand, vertical roller mills (VRM) that have achieved a share of almost 90% and, on (PDF) MPS mills for coal grinding ResearchGateCoolidal Mill For Liquid Coal Colloidal silver is a mineral Colloidal silver products were once available as OTC drug products, but in 1999 the FDA ruled that they aren't safe G Pulverizer With Pulverizing Bowl Dec 30, 2020 Asphalt Pulverizer Process Asphalt pulverizing is the process of grinding up both the top layer of asphalt and its coolidal mill for liquid coal coal russian stolarstwo 2024年5月3日 where ε is the static dielectric constant, n is the refractive index of materials in the visible range, ν e refers to the electronic absorption frequency, k is the Boltzmann constant, T is the temperature, and h is Plank’s constant As reported in the literature [], compared to TiO 2, a typical electrostatic colloidal oxide, the value of the Hamaker constant of SiO 2 (0651 × 10 Understanding the stability behavior of colloidal silica in
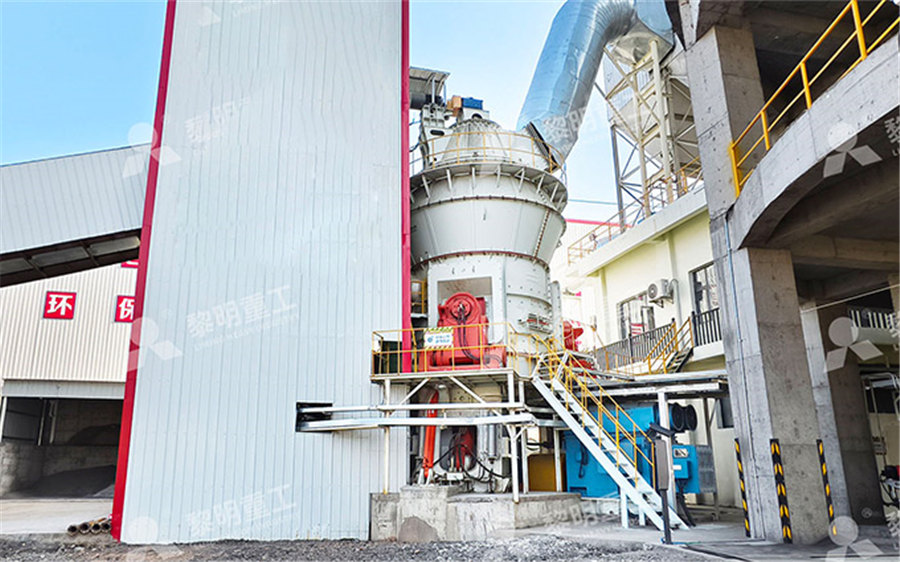
What is “liquid coal”? – JeanMarc Jancovici
2012年7月1日 The answer takes three letters: CTL, for “coal to liquids”, a technology known since the 1920’s, and that allows to turn coal into liquid fuels The basic idea is pretty simple: you take coal (that contains carbon, but has half the proportion of hydrogen that oil has), bring in hydrogen, and at the end you get liquid fuelsCoal can also be liquefied directly, without going through the production of synthesis gas This process is termed coaltoliquid (CTL) and is a reasonably mature technology The process typically uses the technique of heating under pressure (up to 470°C, 200 bar) and hydrogenation where hydrogen is added to a coalwater slurry The slurry CoaltoLiquids an overview ScienceDirect Topics2024年9月28日 Coal mills, essential components in power generation and various industrial processes, pose significant safety risks if not properly managed These mills, used to grind coal into a fine powder for combustion, present potential hazards such as fire, explosion, and mechanical failures This article outlines best practices and precautions to ensure thEnsuring Safety in Coal Mills Coal Mill Safety, Explosion and Coal water slurry ball mill (CWS ball mill) is the key equipment for coal water slurry fuel production, which is commonly used in coal water slurry power plant Coal water slurry ball mill is grinding equipment specially used for coal water slurry production Its specifications, structure and working conditions must meet the requirements of coal water slurry production scale, Coal Water Slurry Ball Mill
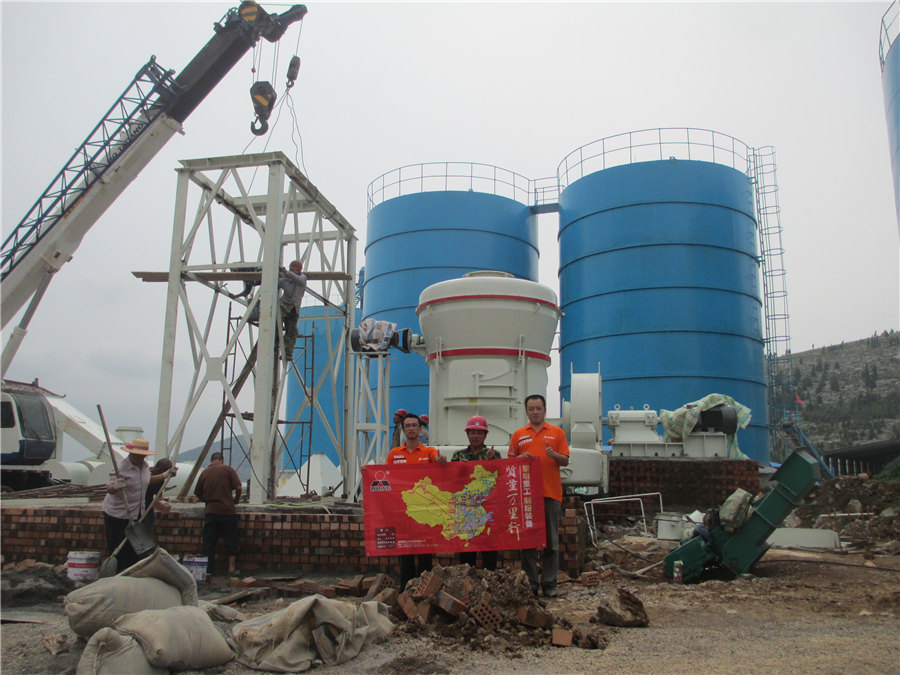
Raymond® Bowl Mill Coperion
The Raymond® Bowl Mill is considered the finest vertical rollermill available for pulverizing coal Each bowl mill system is designed to achieve thebest solution forthe processing application The mill, feeder, classifier, fan, cyclone,dust collector and other system components are selected to meet the requirementsand characteristics of the material processedBiocompatible Mill and grind liquid for dental milling machines Available in 1KG and 5KG containers Related Weight: 26 lbs: Dimensions: 7 × 2 × 2 in: Size: 1L, 5L Brand ImesIcoreimesicore CORiTEC Mill Grind Cooling Liquid ArticonCoal has been mined and used as a source of energy for centuries The first recorded use of coal was in China, with indications that the Chinese began using coal for heating and smelting about 2,500 years ago, and most historians believe that coal was used in various parts of the world 3,000–4,000 years ago during the Bronze Age []A system for mining coal was present in Coal to Liquids Technologies SpringerLinkBased on the characteristics of the startstop timing of coal mills, an economic and flexible return function was designed to evaluate the quality of the startstop timing By utilizing intelligent decisionmaking algorithms, the optimal startstop timing for coal mills was determined and validated through simulation on a certain ultrasupercritical 1000MW unit The results Autonomous Decision Control of StartStop Timing for Coal Mills
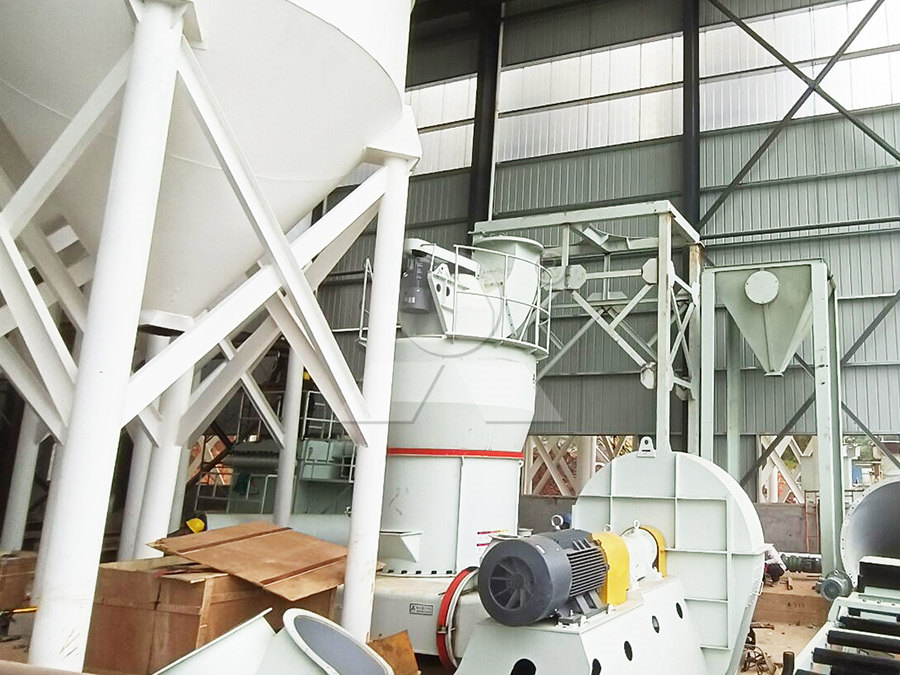
The new liquid–liquid extraction method for separation of
2014年12月29日 Phenolic compounds are mainly derived from coal tar, petroleum, and coal liquefaction oil The traditional acid–base separation method can cause serious environmental problems In this research, imidazole and its homolog compounds were designed as new extraction agents for the separation of phenols from coal tar, which can form deep eutectic 2020年12月21日 The mill reduces the particle size The colloid milling process is perform by adding the heavier liquid to the chamber of the mill which performs the shearing process Once the heavier liquid has been added, the lighter material Working principle of Colloid Mills Promas 2013年9月30日 This study investigates the practicality of using a liquid CO 2 /coal slurry preparation and feed system for the EGas™ gasifier in an integrated gasification combined cycle (IGCC) electric power generation plant configuration Liquid CO 2 has several property differences from water that make it attractive for the coal slurries used in coal gasificationbased power Liquid CO2/Coal Slurry for Feeding Low Rank Coal to 2 The hot air is used for transportation of the recirculating coal within the mill and also for transporting the coal from the pulverizer to the furnace As the coal is continuously reduced in size, the smaller/lighter particles are swept from the Bowl Mill Coal Pulverizer COAL HANDLING

Effective treatment and the valorization of solid and liquid
2021年3月15日 Olive oil extraction processes generate significant quantities of wastes, olive mill solid waste, and olive mill wastewater, which are rich in precious compounds but toxic to the environment In particular, olive mill wastewater is highly toxic As already specified, the direct pyrolysis of a liquid discharge to produce biocoal is a newly A simple energy balance model of the coal mill is derived in (Odgaard and Mataji 2006), this model is based on a more detailed model found in (Rees and Fan 2003)In this model the coal mill is seen as one body with the mass m mThe following variables are defined: T(t) is the temperature in the coal dust flow in the mill, ṁ PA (t) is the primary air mass flow, T PA (t) is Coal Mill an overview ScienceDirect TopicsReliable coal pulverizer performance is essential for sustained fullload operation of today's power plants An effective pulverizer must be capable of handling a wide variety of coals and accommodating load swings in utility boilers as large as 1,300 MW BW's pulverizers, found at power stations throughout the worldReliable Coal Pulverizers and Mills » Babcock WilcoxNext, the levelized cost of directcoaltoliquid is 648–1027 $/t of oil, whereas that of indirectcoaltoliquid is 653–1065 $/t of oil When coupled with the carbon capture utilization and storage technology, the levelized cost of directcoaltoliquid is 285–1364 $/t of oil, compared to 1101–9793 $/t of oil for indirectcoaltoliquidLifecycle carbon footprint and cost assessment for coalto
.jpg)
Pore structure response at different scales in coal to cyclical liquid
2024年5月14日 The methane in the coal seams of abandoned mines is a valuable natural gas resource However, the ultralow permeability of coal seams restricts the extraction of coalbed methane The liquid nitrogen fracturing technology is a novel approach suitable for enhancing the permeability of coal seams in abandoned mines The ultralow temperature could potentially 2023年8月12日 ATOX coal mill Working principles The raw coal enters the mill via a rotary sluice and feed chute and is discharged onto the rotating grinding table The rotation of the table accelerates the flow of material towards the grinding track, where the coal is ground between the table and the three rollers The coal then continues over the damATOX coal mill FLSmidth CementSols are colloidal systems where solid particles are dispersed in a liquid medium Due to Brownian motion, sols have smaller particle sizes that do not settle over time Gels consist of a continuous solid network throughout a liquid medium Colloids: Definition, Characteristics, Types, and 2023年1月1日 14 Solid–liquid separation technologies for coal Author links open overlay panel Gotz Bickert Show more Outline belt, chamber, tube, vibrated bed, pneumatic, pulsed combustion, fluidized bed, vibratory, mill type shaft to moving bed dryers, which could be either tempered with ambient air or with gas/exhaust recirculation while the Solid–liquid separation technologies for coal ScienceDirect
.jpg)
Thin liquid film drainage mechanism for bubble − particle
2024年3月15日 Thin liquid film drainage mechanism for bubble − particle attachment interactions in the lowrank coal flotation in the presence of salt and surfactants The lowrank coal samples were first crushed by a jaw crusher and then drygrinded using a mechanical ball mill After that, the particles were dry sieved to different size fractions A colloid mill is a machine that is used to reduce the particle size of a solid in suspension in a liquid, or to reduce the droplet size of a liquid suspended in another liquid +9179; sales@prismpharmamachinery; MENU MENU About; Products Mixers;Colloid Mill Pharmaceuticals Machinery2024年3月15日 The lowrank coal samples were first crushed by a jaw crusher and then drygrinded using a mechanical ball mill After that, the particles were dry sieved to different size fractions (containing 0–0074 mm, 0074–015 mm and 015–025 mm three parts) Obviously, the stability of the liquid film of coal particles after KCl salt Thin liquid film drainage mechanism for bubble − particle ``` coolidal mill for liquid coalColloidal Fuel Dispersions using Coal,Petroleum Coke and technologies have led to the development of colloidal fuel dispersions using coal,petrolgitsrht
.jpg)
CoaltoLiquid Technology an overview ScienceDirect Topics
Economic analysis of unconventional liquid fuel sources Mehmet Erturk, in Renewable and Sustainable Energy Reviews, 2011 221 Coal to liquid (CTL) Coal is a solid fuel with high carbon content compared to liquids The current liquid fuels which are consumed for the transportation purposes have hydrogen content around 12–15%, whereas coal contains only 5% typically [1]2014年1月1日 Two mill systems are employed for most coal grinding applications in the cement industry These are, on the one hand, vertical roller mills (VRM) that have achieved a share of almost 90% and, on (PDF) MPS mills for coal grinding ResearchGateCoolidal Mill For Liquid Coal Colloidal silver is a mineral Colloidal silver products were once available as OTC drug products, but in 1999 the FDA ruled that they aren't safe G Pulverizer With Pulverizing Bowl Dec 30, 2020 Asphalt Pulverizer Process Asphalt pulverizing is the process of grinding up both the top layer of asphalt and its coolidal mill for liquid coal coal russian stolarstwo 2024年5月3日 where ε is the static dielectric constant, n is the refractive index of materials in the visible range, ν e refers to the electronic absorption frequency, k is the Boltzmann constant, T is the temperature, and h is Plank’s constant As reported in the literature [], compared to TiO 2, a typical electrostatic colloidal oxide, the value of the Hamaker constant of SiO 2 (0651 × 10 Understanding the stability behavior of colloidal silica in